Salesforce Supply Chain: Inventory, Logistics Tracking
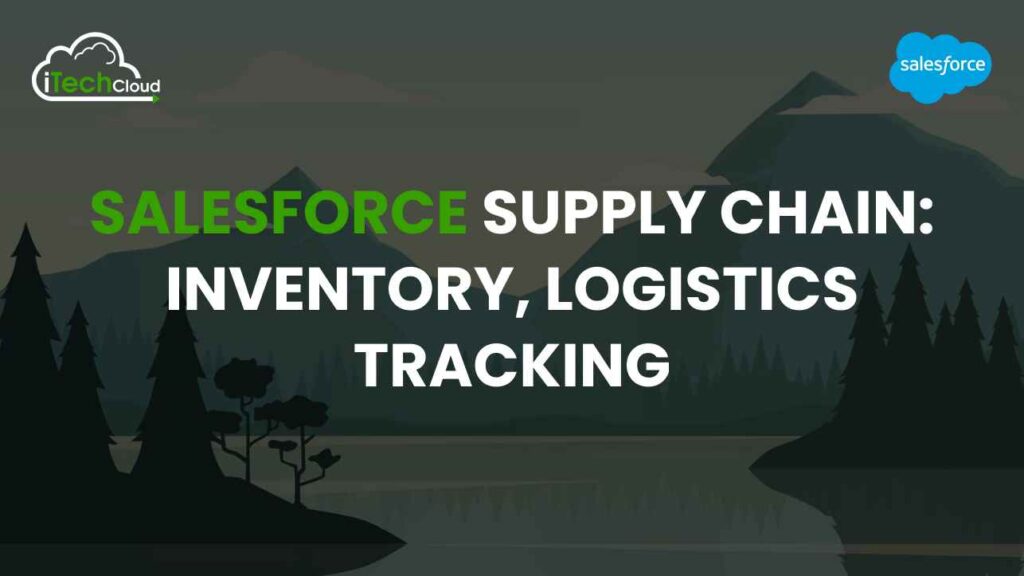
In today’s dynamic business landscape, where supply chains are becoming increasingly complex, organizations are seeking innovative solutions to streamline their operations and stay ahead of the competition. Salesforce, renowned for its customer relationship management (CRM) platform, has expanded its capabilities to cater to the evolving needs of Salesforce Supply Chain management. In this blog post, we’ll delve into how Salesforce is revolutionizing supply chains, empowering businesses to optimize processes, enhance visibility, and drive growth.
Understanding Salesforce Supply Chain
Salesforce Supply Chain management, it’s essential to grasp the intricacies of modern supply chains. Supply chains today are global, interconnected networks involving multiple stakeholders, from suppliers to manufacturers, distributors, retailers, and customers. This complexity often leads to challenges such as inefficient processes, inventory management issues, lack of visibility, and disjointed communication.
Table of Contents
The Role of Salesforce Supply Chain
Salesforce has emerged as a crucial tool in optimizing Salesforce Supply Chain management (SCM), offering a range of capabilities that enhance visibility, efficiency, and collaboration across various supply chain functions. By leveraging its customer relationship management (CRM) strengths, Salesforce helps streamline inventory management, logistics, supplier collaboration, and customer service, enabling businesses to respond swiftly to market demands and improve overall operational effectiveness.
1. Supply Chain Visibility and Transparency
Salesforce provides end-to-end visibility across the supply chain by integrating data from multiple sources into a unified platform. This real-time transparency allows companies to monitor goods movement, manage inventory levels, and oversee production processes effectively. Advanced data analytics and reporting tools help identify bottlenecks, predict potential disruptions, and support proactive decision-making. Enhanced visibility ensures smoother operations and better risk management.
2. Inventory Management
Effective inventory management is essential for meeting customer demands without incurring unnecessary costs. Salesforce automates inventory tracking and management, using predictive analytics to forecast demand accurately. This capability helps businesses maintain optimal stock levels, avoiding overstocking and stockouts. Automated alerts and replenishment processes further streamline inventory management, reducing manual errors and ensuring timely availability of products.
3. Optimizing Logistics and Transportation
Logistics and transportation are critical components of the Salesforce Supply Chain that directly impact efficiency and customer satisfaction. Salesforce provides tools for route planning, carrier selection, and shipment tracking, often integrated with transportation management systems (TMS). Real-time tracking features enable businesses to monitor shipments, ensuring timely deliveries and providing accurate updates to customers. By optimizing logistics operations, companies can reduce transit times, lower costs, and improve service quality.
4. Supplier and Partner Collaboration
Collaboration with suppliers and partners is crucial for a seamless Salesforce Supply Chain. Salesforce offers a unified platform for sharing information, communication, and coordination among all stakeholders. Its cloud-based nature allows easy access to information from any location, fostering better collaboration and reducing lead times. Streamlined interactions with suppliers and partners improve procurement processes and overall supply chain agility, ensuring everyone is aligned and working towards common goals.
5. Improving Customer Service and Satisfaction
Customer service is a vital aspect of SCM that impacts customer satisfaction and loyalty. Salesforce’s CRM capabilities enable companies to integrate customer data with Salesforce Supply Chain operations, facilitating personalized service, prompt issue resolution, and timely order fulfillment. Case management and customer support tools help resolve complaints and queries efficiently, enhancing overall customer satisfaction. By delivering consistent and high-quality service, businesses can build stronger customer relationships.
6. Artificial Intelligence and Machine Learning
Salesforce incorporates artificial intelligence (AI) and machine learning (ML) through its Einstein Analytics platform, offering advanced predictive capabilities for SCM. AI and ML analyze large datasets to identify patterns and trends, providing insights that might not be immediately apparent. Predictive analytics can forecast demand, optimize pricing strategies, and anticipate Salesforce Supply Chain disruptions before they occur. These insights enable proactive issue resolution, improved planning accuracy, and better decision-making processes.
7. Customization and Scalability
One of Salesforce’s key strengths is its customization and scalability. The platform can be tailored to meet the specific needs of different industries and businesses, with customizable dashboards, reports, and workflows. As businesses grow, Salesforce can scale to support additional users and functionalities, integrating seamlessly with other systems. This flexibility ensures that Salesforce can adapt to evolving business needs, providing a robust solution for dynamic Salesforce Supply Chain challenges.
8. Integration with Other Technologies
Salesforce’s ability to integrate with other technologies enhances its role in SCM. Through the AppExchange marketplace, businesses can deploy various third-party applications that extend Salesforce’s functionalities. Integrations with enterprise resource planning (ERP) systems, warehouse management systems (WMS), and internet of things (IoT) devices create a connected supply chain ecosystem. These integrations ensure seamless data flow across different systems, improving overall efficiency and accuracy.
Key Features and Capabilities of Salesforce Supply Chain
Salesforce, a prominent customer relationship management (CRM) platform, offers a multitude of features and capabilities that significantly enhance Salesforce Supply Chain management (SCM). By integrating comprehensive data management, advanced analytics, automation, and collaboration tools, Salesforce optimizes various supply chain processes, including inventory management, logistics, supplier collaboration, and customer service.
Below are the key features and capabilities of Salesforce that contribute to efficient supply chain operations.
1. Comprehensive Data Integration and Visibility
Salesforce excels in data integration, bringing together information from various sources into a single, unified platform. This holistic view of the supply chain allows for real-time monitoring and management of operations. Stakeholders can track the movement of goods, monitor inventory levels, and oversee production processes seamlessly. Enhanced data visibility helps identify inefficiencies, predict potential disruptions, and support informed decision-making.
2. Advanced Analytics and Reporting
Salesforce’s robust analytics and reporting tools provide deep insights into supply chain performance. Users can create customizable dashboards and reports that display key performance indicators (KPIs) and metrics relevant to their operations. Advanced analytics enable companies to perform root cause analysis, identify trends, and make data-driven decisions. These tools are crucial for continuous improvement and strategic planning within the supply chain.
3. Predictive Analytics and Forecasting
Through its Einstein Analytics platform, Salesforce incorporates artificial intelligence (AI) and machine learning (ML) to offer predictive analytics and forecasting capabilities. These advanced technologies analyze historical data to predict future trends, such as demand fluctuations, inventory needs, and potential supply chain disruptions. By leveraging predictive analytics, companies can anticipate challenges and opportunities, optimize inventory levels, and enhance overall supply chain resilience.
4. Automation and Workflow Management
Salesforce Supply Chain processes, reducing manual intervention and increasing efficiency. Workflow automation tools allow users to set up automated alerts, approval processes, and task assignments. For example, when inventory levels fall below a certain threshold, an automated alert can trigger a replenishment order. Automation minimizes errors, speeds up processes, and ensures that critical tasks are completed on time.
5. Inventory Management
Effective inventory management is crucial for maintaining the right balance of stock to meet customer demands without incurring excess costs. Salesforce provides tools for real-time inventory tracking, automated replenishment, and demand forecasting. By utilizing these tools, companies can maintain optimal stock levels, reduce the risk of overstocking or stockouts, and ensure timely product availability. Inventory management capabilities are further enhanced by integration with warehouse management systems (WMS).
6. Logistics and Transportation Management
Salesforce supports logistics optimization by providing tools for route planning, carrier selection, and shipment tracking. Integration with transportation management systems (TMS) enables companies to choose the most efficient and cost-effective shipping methods. Real-time tracking features allow businesses to monitor the status of shipments, ensuring timely deliveries and providing customers with accurate delivery updates. This capability helps in reducing transit times, lowering logistics costs, and improving service reliability.
7. Supplier and Partner Collaboration
Collaboration with suppliers and partners is essential for a streamlined supply chain. Salesforce offers a unified platform where all stakeholders can share information, communicate, and coordinate activities. The platform’s cloud-based nature allows easy access to information from any location, facilitating better communication and collaboration. Enhanced collaboration leads to reduced lead times, improved procurement processes, and greater supply chain agility.
8. Customer Service and Relationship Management
Customer service is a critical component of Salesforce Supply Chain management, impacting customer satisfaction and loyalty. Salesforce’s CRM capabilities enable companies to integrate customer data with supply chain operations, providing personalized service, prompt issue resolution, and timely order fulfillment. Tools for case management and customer support help resolve complaints and queries efficiently, enhancing overall customer satisfaction and strengthening customer relationships.
9. Customization and Scalability
Salesforce is highly customizable and scalable, allowing businesses to tailor the platform to their specific needs. Customizable dashboards, reports, and workflows enable companies to create a supply chain management system that aligns with their unique requirements. As businesses grow, Salesforce can scale to support additional users and functionalities, ensuring continuous alignment with evolving business needs. This flexibility makes Salesforce a versatile solution for companies of all sizes and industries.
10. Integration with Third-Party Applications
Salesforce’s ability to integrate with third-party applications further enhances its functionality. Through the AppExchange marketplace, businesses can deploy various applications that complement and extend Salesforce’s capabilities. Integrations with enterprise resource planning (ERP) systems, warehouse management systems (WMS), and internet of things (IoT) devices create a connected and cohesive supply chain ecosystem. These integrations ensure seamless data flow across different systems, improving overall efficiency and accuracy.
Real-World Examples of Salesforce Supply Chain
Salesforce has been widely adopted across various industries to enhance supply chain management (SCM). Real-world examples demonstrate its capabilities in improving inventory management, logistics, supplier collaboration, and customer service. These examples highlight how companies leverage Salesforce to drive efficiency, visibility, and agility in their supply chain operations.
1. Coca-Cola: Streamlining Bottling Operations
Coca-Cola Bottling Company uses Salesforce to streamline its extensive bottling and distribution network. By integrating Salesforce with its existing systems, Coca-Cola can monitor inventory levels in real-time, ensuring timely replenishment and reducing stockouts. The platform’s analytics capabilities enable Coca-Cola to forecast demand more accurately, adjust production schedules, and optimize distribution routes. This integration enhances operational efficiency and ensures that products are delivered to retailers and customers promptly.
2. L’Oréal: Enhancing Supplier Collaboration
L’Oréal, a global leader in beauty products, leverages Salesforce to enhance collaboration with its suppliers. Salesforce’s cloud-based platform allows L’Oréal to maintain transparent and efficient communication with suppliers worldwide. By sharing real-time data on inventory levels, production schedules, and shipment status, L’Oréal ensures that suppliers are aligned with its operational needs. This collaboration reduces lead times, improves procurement processes, and enhances overall Salesforce Supply Chain agility.
3. Schneider Electric: Improving Logistics and Customer Service
Schneider Electric, a global specialist in energy management and automation, uses Salesforce to optimize its logistics and enhance customer service. Salesforce’s integration with Schneider Electric’s transportation management system (TMS) allows for efficient route planning and carrier selection. Real-time shipment tracking provides customers with accurate delivery updates, improving transparency and satisfaction. Additionally, Salesforce’s CRM capabilities enable Schneider Electric to manage customer interactions more effectively, resolving issues promptly and ensuring timely order fulfillment.
4. Dell: Optimizing Inventory Management
Dell Technologies employs Salesforce to optimize its complex inventory management processes. By integrating Salesforce with its ERP system, Dell gains real-time visibility into inventory levels across multiple warehouses and distribution centers. Predictive analytics tools help Dell forecast demand accurately and adjust inventory levels accordingly. This capability minimizes overstocking and stockouts, ensuring that products are available when and where they are needed. Automated alerts and replenishment processes further streamline inventory management, reducing manual intervention and errors.
5. Toyota: Enhancing Dealer and Customer Relations
Toyota utilizes Salesforce to strengthen its relationships with dealers and customers. Salesforce’s CRM platform provides Toyota with a unified view of customer interactions and dealer performance. By integrating customer and dealer data with its supply chain operations, Toyota can offer personalized service, address issues quickly, and ensure timely delivery of vehicles and parts. This integration enhances customer satisfaction and loyalty, as well as dealer efficiency.
Benefits of Using Salesforce Supply Chain
Salesforce, a premier customer relationship management (CRM) platform, brings numerous benefits to Salesforce Supply Chain management (SCM) through its advanced features and capabilities. By leveraging real-time data, predictive analytics, automation, and robust collaboration tools, Salesforce helps businesses enhance their supply chain operations from end to end.
Here is a step-by-step breakdown of the key benefits of using Salesforce in supply chain management.
1. Visibility and Transparency
Unified Data Integration: Salesforce integrates data from various sources into a single platform, providing a comprehensive view of the Salesforce Supply Chain. This real-time visibility allows stakeholders to monitor inventory levels, track the movement of goods, and oversee production processes effectively.
Real-Time Monitoring: With real-time data updates, companies can identify and address potential issues quickly. Enhanced transparency helps in anticipating disruptions and making informed decisions to optimize operations.
Data Analytics and Reporting: Salesforce offers robust analytics and reporting tools that help businesses track key performance indicators (KPIs) and gain insights into supply chain performance. Customizable dashboards and reports enable continuous monitoring and strategic planning.
2. Improved Inventory Management
Automated Inventory Tracking: Salesforce automates the tracking of inventory levels, ensuring that stock is maintained at optimal levels. This reduces the risk of overstocking and stockouts, which can impact customer satisfaction and increase holding costs.
Predictive Analytics: The platform’s predictive analytics capabilities forecast demand accurately, allowing businesses to adjust inventory levels proactively. This ensures that products are available when needed, reducing the likelihood of shortages or excess stock.
Automated Replenishment: Automated alerts and replenishment processes streamline inventory management. When inventory levels fall below a certain threshold, an automated alert triggers a replenishment order, minimizing manual intervention and errors.
3. Optimized Logistics and Transportation
Route Planning and Carrier Selection: Salesforce supports logistics optimization by providing tools for efficient route planning and carrier selection. This ensures that goods are transported via the most cost-effective and timely routes.
Real-Time Shipment Tracking: Real-time tracking features enable businesses to monitor the status of shipments, ensuring timely deliveries. Customers receive accurate delivery updates, improving transparency and satisfaction.
Integration with TMS: Integration with transportation management systems (TMS) helps in selecting the most efficient shipping methods, reducing transit times, and lowering logistics costs.
4. Supplier and Partner Collaboration
Unified Communication Platform: Salesforce offers a unified platform for sharing information, communication, and coordination among suppliers and partners. This cloud-based system allows easy access to information from any location, fostering better collaboration.
Reduced Lead Times: By streamlining interactions with suppliers and partners, Salesforce helps reduce lead times and improve procurement processes. Enhanced collaboration ensures that all parties are aligned and working towards common goals, increasing overall supply chain agility.
5. Superior Customer Service and Relationship Management
Integrated Customer Data: Salesforce’s CRM capabilities enable the integration of customer data with supply chain operations. This facilitates personalized service, prompt issue resolution, and timely order fulfillment.
Case Management and Support: Tools for case management and customer support help resolve complaints and queries efficiently. Enhanced customer service builds stronger relationships and fosters long-term loyalty.
Customer Satisfaction: Consistent and high-quality service delivery improves customer satisfaction. By ensuring timely and accurate fulfillment of orders, businesses can enhance their reputation and customer trust.
6. Predictive Analytics and Proactive Decision-Making
AI and Machine Learning: Salesforce incorporates artificial intelligence (AI) and machine learning (ML) through its Einstein Analytics platform. These technologies analyze large datasets to identify patterns and trends.
Forecasting and Risk Mitigation: Predictive analytics can forecast demand, optimize pricing strategies, and anticipate supply chain disruptions. These insights allow for proactive decision-making, helping businesses address potential issues before they escalate.
7. Automation and Efficiency
Workflow Automation: Salesforce Supply Chain processes, reducing manual intervention and increasing efficiency. Automated workflows ensure that critical tasks are completed on time and minimize the risk of human error.
Efficiency Gains: By automating routine tasks, businesses can focus on strategic activities, improving overall operational efficiency and productivity.
8. Customization and Scalability
Tailored Solutions: Salesforce’s customization capabilities allow businesses to tailor the platform to their specific needs. Customizable dashboards, reports, and workflows enable the creation of a Salesforce Supply Chain management system that aligns with unique business requirements.
Scalability: As businesses grow, Salesforce can scale to support additional users, expand functionalities, and integrate seamlessly with other systems. This flexibility ensures that Salesforce can adapt to evolving business needs.
9. Integration with Third-Party Applications
AppExchange Marketplace: Salesforce’s AppExchange marketplace offers a variety of third-party applications that extend its capabilities. Integrations with enterprise resource planning (ERP) systems, warehouse management systems (WMS), and internet of things (IoT) devices create a connected supply chain ecosystem.
Seamless Data Flow: These integrations ensure seamless data flow across different systems, improving overall efficiency and accuracy in supply chain operations.
Conclusion:
Salesforce Supply Chain management (SCM) by integrating comprehensive data visibility, advanced analytics, automation, and robust collaboration tools. Key benefits include improved inventory management, optimized logistics, and enhanced supplier and partner collaboration. Real-time data and predictive analytics facilitate proactive decision-making, while automation streamlines processes and reduces errors. Customization and scalability ensure that Salesforce can be tailored to meet specific business needs and grow with the company.
However, challenges such as system integration, cost considerations, user adoption, data security, and change management must be addressed for a successful implementation. Strategic planning, effective training, and robust security measures are crucial. By overcoming these challenges, businesses can fully leverage Salesforce to achieve greater efficiency, agility, and strategic advantage in their supply chain operations, ultimately enhancing customer satisfaction and operational excellence.